UV Curable Resin: All You Need to Know
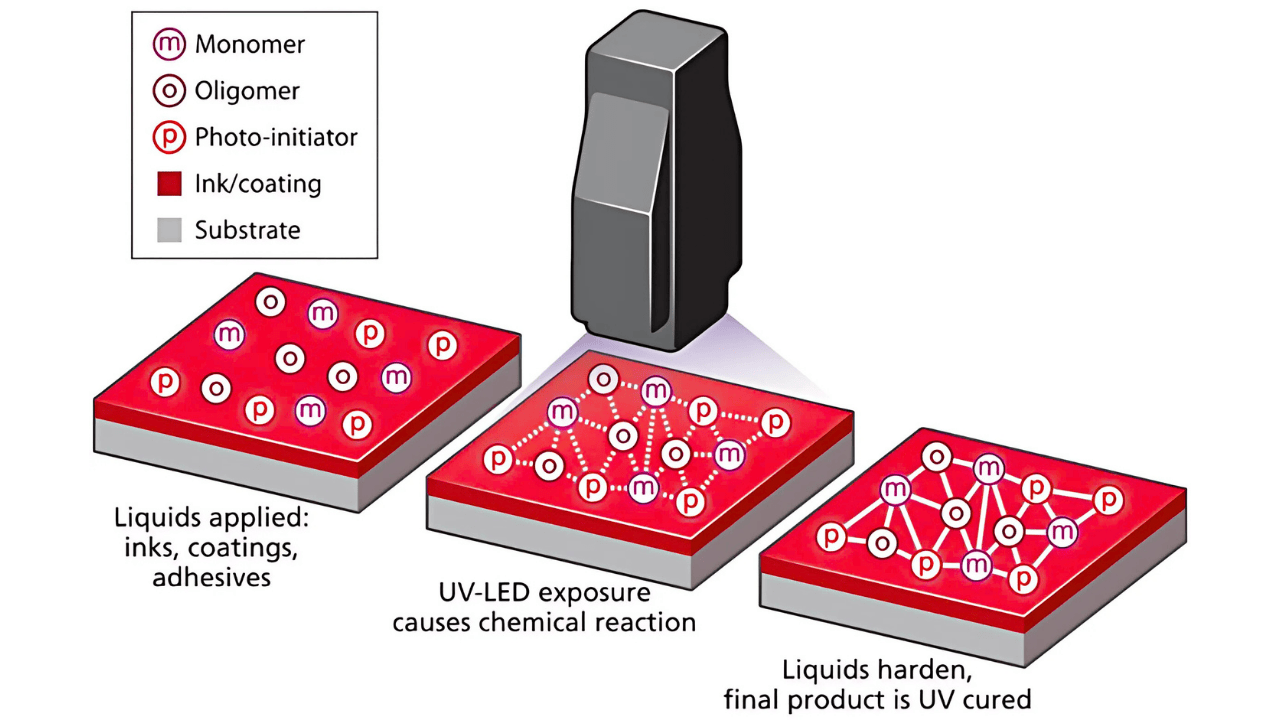
UV curable resin refers to materials that undergo rapid polymerization and solidification when exposed to ultraviolet (UV) light. This unique curing mechanism distinguishes UV curable resins from conventional resins that rely on heat, chemical reactions, or air drying for curing. UV curing offers numerous advantages, including faster production times, reduced energy consumption, enhanced environmental sustainability, and improved product performance.
UV curable resins find widespread applications across various industries, including coatings, adhesives, printing, electronics, and medical devices. Their versatility and compatibility with different substrates make them indispensable in modern manufacturing. UV curable resins are crucial in advancing technology and innovation across multiple sectors, from providing durable surface finishes to enabling intricate 3D printing.
Let’s learn the important aspects of UV cureable resins.
Composition and Chemical Structure
UV curable resins are formulated using a combination of oligomers, monomers, photoinitiators, and additives. Each component contributes to the overall properties and performance of the resin, ensuring optimal curing behavior and end-product characteristics.
- Oligomers: Oligomers are long-chain polymers with reactive functional groups that facilitate crosslinking during UV curing. These pre-polymerized molecules provide the backbone structure for the cured resin, imparting mechanical strength, flexibility, and other desired properties. Common oligomers in UV curable resins include acrylics, epoxies, polyesters, and urethanes.
- Monomers: Monomers are small, reactive molecules that participate in the crosslinking reactions initiated by UV light. They help increase the resin’s viscosity, improve adhesion, and adjust the curing speed. Methacrylates, acrylates, and vinyl ethers are monomers commonly employed in UV curable formulations.
- Photoinitiators: These compounds absorb UV light and initiate polymerization by generating free radicals or cationic species. They play a crucial role in initiating the crosslinking reactions between oligomers and monomers, leading to the rapid curing of the resin. Photoinitiators are selected based on their compatibility with the resin system and the specific wavelength of UV light used for curing.
- Additives: As stabilizers, antioxidants, plasticizers, and pigments may be incorporated into UV curable resin formulations to modify their properties and enhance performance. Stabilizers help prevent premature curing or degradation of the resin during storage, while antioxidants protect against thermal and oxidative degradation. Plasticizers improve flexibility, and pigments provide coloration for coatings and inks.
Mechanism of UV Curing
UV curing involves a photochemical reaction initiated by ultraviolet (UV) light exposure. This process occurs in several distinct steps:
- Absorption of UV Light: UV curable resins contain photoinitiators, molecules capable of absorbing UV radiation. When exposed to UV light of specific wavelengths, these photoinitiators become excited and undergo photolysis, breaking down into free radicals or cationic species.
- Initiation: The free radicals or cationic species generated by photolysis initiate resin polymerization. They react with the double bonds in the oligomers and monomers, forming reactive intermediates known as radicals or cations.
- Propagation: The reactive intermediates undergo a chain reaction known as propagation, where they continue to react with additional oligomers and monomers. This results in the formation of longer polymer chains and the crosslinking of adjacent molecules.
- Termination: Eventually, the polymerization process reaches a point where all reactive sites are consumed, leading to the termination of the reaction. The resin is fully cured at this stage, forming a solid polymer network.
Properties of UV Curable Resin
UV curable resins exhibit several unique properties that make them highly desirable for a wide range of applications:
Rapid Curing: UV curable resins offer faster curing times than traditional curing methods. Curing within seconds to minutes increases production throughput and shorter lead times. This rapid curing also reduces energy consumption and improves overall process efficiency.
Chemical Resistance: UV curable resins exhibit excellent resistance to chemicals, including acids, bases, solvents, and oils. This chemical resistance makes them ideal for applications requiring durability and protection against harsh environments, such as automotive parts, electronic components, and industrial machinery coatings.
Adhesion Properties: UV curable resins demonstrate superior adhesion to various substrates, including metals, plastics, glass, ceramics, and composites. This strong adhesion ensures robust bonding in various applications, such as bonding dissimilar materials, laminating films, and encapsulating electronic components.
Versatility in Formulation: UV curable resins offer versatility in formulation, allowing for customization of properties to meet specific application requirements. Formulators can adjust viscosity, flexibility, hardness, and cure speed by selecting appropriate oligomers, monomers, photoinitiators, and additives. This versatility enables the development of tailored solutions for diverse industries, including coatings, adhesives, 3D printing, and electronics manufacturing.
Overall, the unique combination of rapid curing, environmental friendliness, chemical resistance, adhesion properties, and versatility in formulation makes UV curable resins highly attractive for a wide range of industrial applications. Continued advancements in formulation chemistry and curing technologies are expected to expand the utility and adoption of UV curable resins across various sectors further.
Types of UV Curable Resins
UV curable resins encompass a variety of formulations tailored to specific applications and performance requirements. Each type of UV curable resin offers unique properties and characteristics, making them suitable for diverse industrial uses. The most common UV curable resins include acrylic, epoxy, polyester, and urethane-based resins.
Acrylic-Based Resins
Acrylic-based UV curable resins are widely used in coatings, adhesives, and printing inks due to their excellent clarity, weatherability, and chemical resistance. These resins are formulated from acrylic oligomers and monomers, which undergo rapid crosslinking upon exposure to UV light. Acrylic-based resins offer high gloss, good adhesion to various substrates, and exceptional durability, making them suitable for high-performance coatings, such as automotive finishes, wood coatings, and decorative laminates.
Epoxy-Based Resins
Epoxy-based UV curable resins are characterized by their high mechanical strength, chemical resistance, and adhesion properties. These resins are formulated from epoxy oligomers and monomers, which crosslink via cationic polymerization upon UV exposure. Epoxy-based resins are commonly used in electronic encapsulation, coatings for metal and concrete surfaces, and structural adhesives due to their excellent adhesion to substrates and resistance to harsh environments.
Polyester-Based Resins
Polyester-based UV curable resins are versatile materials with many applications, including coatings, composites, and 3D printing. These resins are formulated from unsaturated polyester oligomers and monomers, which undergo free radical polymerization upon UV exposure. Polyester-based resins offer flexibility, chemical resistance, and adhesion properties, making them suitable for fiberglass reinforcement, automotive clear coats, and architectural coatings.
Urethane-Based Resins
Urethane-based UV curable resins combine the advantages of urethane chemistry with the rapid curing capabilities of UV technology. These resins are formulated from urethane oligomers and monomers, which undergo crosslinking via free radical polymerization upon UV exposure. Urethane-based resins offer excellent flexibility, abrasion resistance, and adhesion to substrates, making them ideal for applications such as flexible coatings, elastomers, and adhesives in the automotive, aerospace, and consumer electronics industries.
Applications of UV Curable Resin
UV curable resin finds wide-ranging applications across various industries due to its rapid curing, environmental friendliness, and excellent performance properties. Some of the key applications include:
Coatings and Finishes: UV curable resin is extensively used in the coatings and finishing industry for various substrates including wood, plastic, metal, and glass. It provides durable, high-gloss finishes with excellent resistance to abrasion, chemicals, and UV degradation. Applications include automotive coatings, wood furniture finishes, architectural coatings, and protective coatings for electronic devices.
Adhesives and Sealants: UV curable resin is an efficient adhesive and sealant in various industries due to its fast curing speed and strong bond strength. It is used for bonding substrates such as glass, plastics, metals, and ceramics in applications ranging from electronics assembly to medical device manufacturing. UV curable adhesives offer high transparency, flexibility, and resistance to temperature and chemicals.
Printing and Packaging: In the printing and packaging industry, UV curable resin is used in UV offset printing, flexographic printing, and screen printing processes. It enables high-speed printing with sharp image quality, vibrant colors, and instant curing, resulting in fast production turnaround times. UV-curable inks and coatings are also applied in packaging materials to enhance aesthetics, durability, and brand appeal.
Electronics Manufacturing: UV curable resin is critical for encapsulating, bonding, and protecting electronic components. It is used in applications such as conformal coatings for circuit boards, encapsulation of LEDs, bonding of display screens, and potting of sensors. UV-curable materials offer excellent adhesion, thermal stability, and protection against moisture and environmental contaminants.
Dental and Medical Applications: In the dental and medical fields, UV curable resin is utilized for various applications including dental restorations, orthodontic appliances, medical adhesives, and surgical implants. UV-curable materials offer biocompatibility, ease of use, and precise curing, making them suitable for fabricating dental crowns, bridges, splints, and medical devices with intricate geometries.
3D Printing: UV curable resin is preferred for stereolithography (SLA) and digital light processing (DLP) 3D printing technologies. It enables the rapid prototyping of complex parts with high resolution, accuracy, and smooth surface finish. UV-curable resins are used in various industries including automotive, aerospace, consumer goods, and healthcare for producing prototypes, functional parts, and customized products.
Challenges and Limitations
- Substrate Sensitivity: UV curing is effective on transparent substrates with UV-transmissive properties, limiting its applicability to certain materials.
- Depth of Cure: UV light penetration depth restricts the curing thickness of UV-curable materials, requiring multiple passes or specialized curing techniques for thicker layers.
- Equipment Cost: UV curing equipment and lamps can be expensive, especially for large-scale industrial applications, requiring significant initial investment.
- Health and Safety: UV light exposure poses potential health risks to operators, requiring proper safety measures and protective equipment.
- Formulation Complexity: Formulating UV curable resin requires expertise to achieve desired properties and performance, leading to formulation challenges and outcome variability.
Future Trends in UV Curable Materials
The future of UV curable resin is promising, driven by ongoing research, technological advancements, and evolving market demands. Several key trends are expected to shape the future of UV curable resin technology:
Sustainability: The demand for sustainable and eco-friendly materials drives the development of bio-based UV curable resins derived from renewable sources. These materials offer environmental benefits and align with the growing industry emphasis on sustainability.
Functional Additives: A growing focus is on incorporating functional additives into UV curable resin formulations to enhance properties such as antimicrobial activity, self-healing capabilities, and flame retardancy. These additives expand the application possibilities of UV curable resins in diverse fields such as healthcare, electronics, and automotive.
Digital Integration: Integrating UV curable resin technology with digital printing and additive manufacturing processes is expected to revolutionize production methods. This convergence enables customization, on-demand manufacturing, and the creation of complex, high-value products with precision and efficiency.
Smart Materials: Advances in material science are leading to the development of smart UV curable resins with responsive properties, such as stimuli-responsive behavior, shape memory effects, and tunable mechanical properties. These smart materials hold potential for applications in electronics, robotics, and biomedical engineering.
Conclusion
UV curable resin has emerged as a versatile and sustainable material with wide-ranging industry applications. Its rapid curing, environmental friendliness, and superior performance properties make it a preferred choice for coatings, adhesives, 3D printing, electronics, healthcare, and more. As technological advancements continue to drive innovation in UV curable resin formulations and curing processes, the future holds immense potential for further expansion and diversification of its applications.
From bio-based formulations to smart materials and digital integration, the evolution of UV curable resin technology is poised to address emerging market needs while pushing the boundaries of manufacturing capabilities. By leveraging these trends and embracing sustainable practices, UV curable resin is set to play a pivotal role in shaping the future of manufacturing, offering efficient, high-performance solutions for diverse industrial applications.
0 Comments