Electron Beam Machining in Precision Engineering
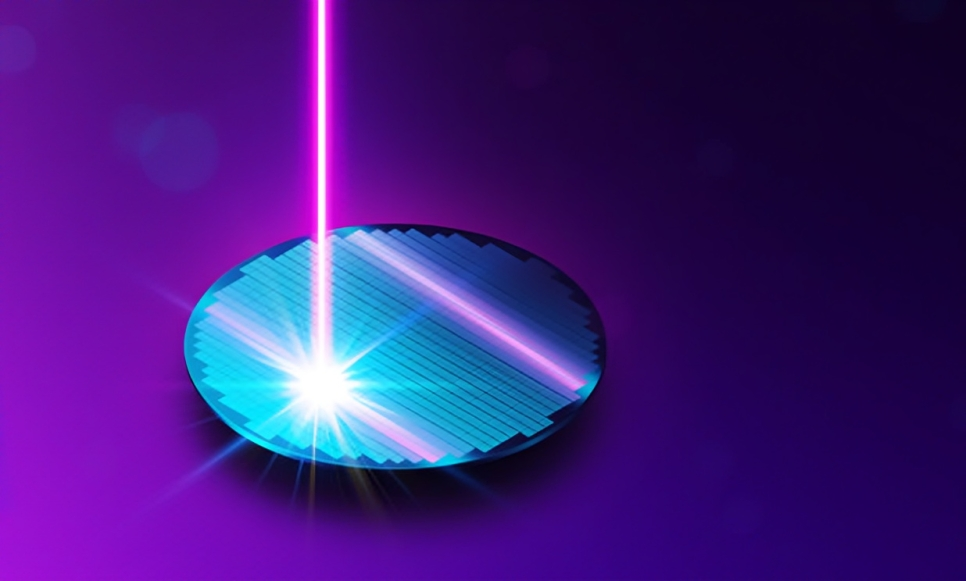
Precision engineering demands cutting-edge technologies that can deliver high accuracy and intricate detailing. Electron Beam Machining (EBM) is a prime example of advanced manufacturing techniques designed to meet the exacting requirements of precision engineering. This article explores the diverse applications of Electron Beam Machining and its pivotal role in achieving precision in manufacturing processes.
What is Electron Beam Machining?
Electron Beam Machining is a non-traditional process that utilizes a high-velocity, focused electron beam to remove material from a workpiece. In EBM, electrons are accelerated to near-light speeds and focused using magnetic lenses, allowing for precise and controlled material removal. This technique is particularly well-suited for applications where traditional methods may fail to achieve the required precision.
Working Principle of Electron Beam Machining (EBM)
Electron Beam Machining (EBM) is a non-traditional process that utilizes a high-velocity, focused electron beam to remove material from a workpiece. The process involves the following key steps:
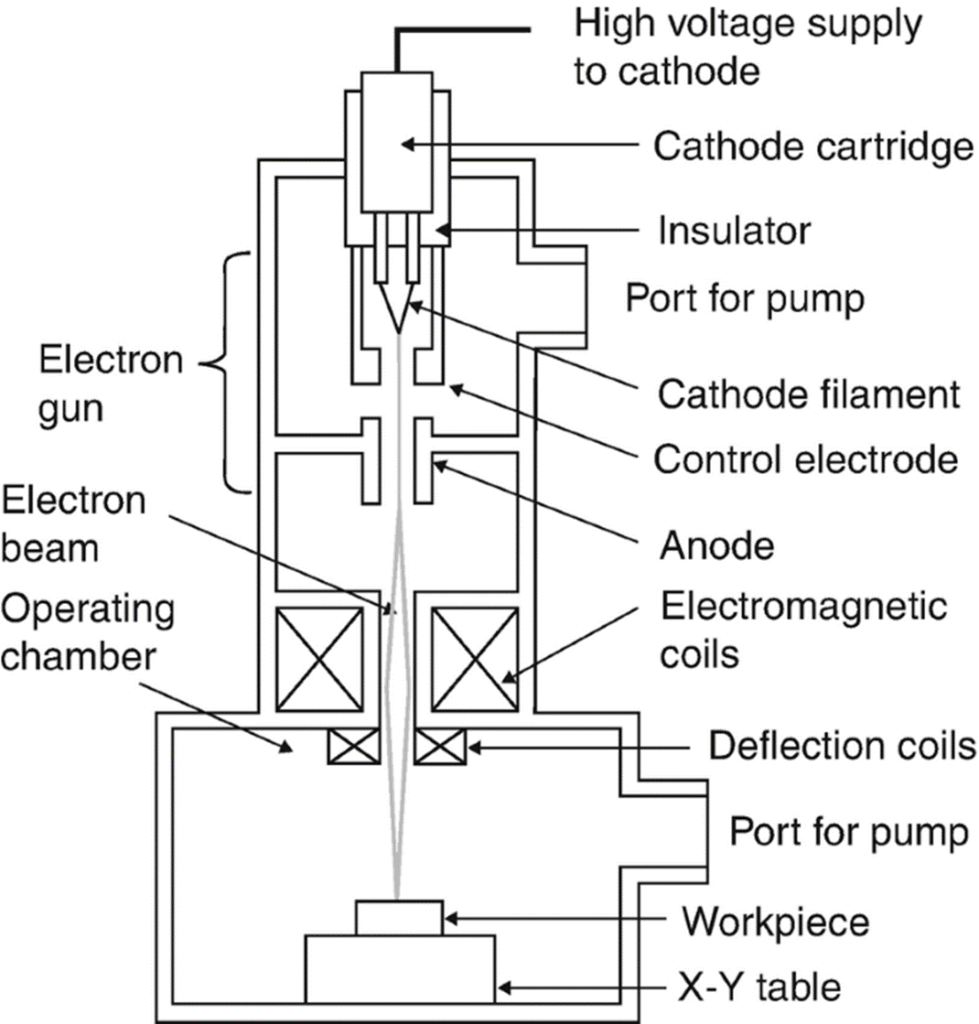
- Electron Generation: Electrons are generated by a cathode through thermionic emission. This involves heating the cathode, causing electrons to be emitted. The cathode is typically made of tungsten due to its high melting point and good electron emission characteristics.
- Electron Acceleration: The emitted electrons are accelerated by an anode by applying a high voltage. This voltage, often in the range of 40-150 kV, imparts high kinetic energy to the electrons, accelerating to nearly the speed of light.
- Focusing: Magnetic lenses or electromagnetic fields focus the high-velocity electrons into a narrow beam. This focused electron beam can achieve spot sizes on the order of micrometers, allowing for precise material removal.
- Material Removal: The focused electron beam is directed onto the workpiece surface. When the high-energy electrons strike the material, they transfer their kinetic energy, leading to localized heating and vaporization. This process, known as electron bombardment, causes the material to be removed from the workpiece.
- Controlling the Beam: Electromagnetic lenses and deflectors can precisely control the electron beam. This control allows for intricate machining patterns and precise material removal according to the desired shape.
- Environment: EBM is typically performed in a vacuum or low-pressure environment to prevent the scattering of electrons and to minimize interactions with air molecules. This enhances the accuracy of the machining process.
Processing Parameters in Electron Beam Machining
- Beam Current: The current of the electron beam is a crucial parameter. It determines the quantity of electrons striking the workpiece per unit time, influencing the material removal rate.
- Acceleration Voltage: The voltage that accelerates the electrons determines their kinetic energy. Higher acceleration voltages result in higher energy electrons and increased material removal rates.
- Beam Focus: The focus of the electron beam, controlled by magnetic lenses, influences the spot size and precision of machining. Smaller spot sizes lead to higher precision but may also result in slower material removal rates.
- Beam Deflection: Electromagnetic deflectors control the movement of the electron beam, enabling complex machining patterns. Precise control of beam deflection is crucial for achieving complex shapes.
- Workpiece Material: The type of material being machined influences the effectiveness of EBM. Conductive materials are more suitable for efficient material removal.
- Environmental Conditions: The machining environment, typically a vacuum or low-pressure chamber, is critical for preventing electron scattering and ensuring accurate machining.
Understanding and optimizing these parameters are essential for achieving the desired precision and efficiency in Electron Beam Machining processes. As technology evolves, advancements in control systems and equipment design will likely contribute to overcoming some of the current limitations associated with EBM.
Applications of EBM in Precision Engineering
- Micro-Machining of Small Components: EBM excels in micro-machining applications, allowing for fabricating extremely small components with intricate details. This is crucial in industries such as electronics and medical devices where miniaturization is a key requirement.
- Precision Cutting of Aerospace Components: In the aerospace industry, where precision and lightweight components are paramount, EBM is employed to cut intricate shapes precisely in materials like titanium and nickel alloys. This ensures the production of aerospace components with tight tolerances and high strength-to-weight ratios.
- Manufacture of Injection Molds: Precision engineering often involves the production of injection molds for the mass production of complex plastic components. EBM is employed to create intricate mold cavities with high precision, reducing the need for secondary machining processes.
- Tool and Die Manufacturing: EBM plays a crucial role in fabricating precision tools and dies used in various manufacturing processes. The high precision and minimal heat-affected zones make EBM suitable for creating sharp cutting edges and intricate shapes in tool and die production.
- Prototyping in the Automotive Industry: Rapid prototyping is essential for design validation and testing in the automotive industry. EBM allows for the quick and precise prototyping of components, aiding in developing high-performance and aerodynamic automotive designs.
- Surface Texturing for Tribological Applications: EBM is employed for surface texturing applications, especially in tribological systems. Texturing surfaces at the micro or nano-level can enhance lubrication, reduce friction, and improve the overall performance and durability of components in machines and engines.
- Fabrication of Optical Components: Precision optics demand meticulous manufacturing processes. EBM is used to fabricate optical components such as lenses and mirrors with intricate shapes and precise surface finishes, meeting the stringent requirements of optical systems.
Advantages of EBM in Precision Engineering
- High Precision: EBM offers exceptionally high precision, making it suitable for applications where tight tolerances and intricate detailing are critical.
- Minimal Heat-Affected Zone: The non-contact nature of EBM results in minimal heat transfer to the workpiece, reducing the heat-affected zone and minimizing thermal distortion.
- Material Versatility: EBM can be applied to various materials, including metals, ceramics, and composites, providing versatility in precision engineering applications.
- Reduced Post-Processing: The accuracy of EBM often reduces the need for extensive post-processing, contributing to time and cost savings in manufacturing.
What is the Difference between Electron Beam Machining and Laser Beam Machining?
The table provides a comprehensive overview of the differences between Electron Beam Machining (EBM) and Laser Beam Machining (LBM). Let’s explore some key aspects to understand the distinctions better:
Parameter | Electron Beam Machining (EBM) | Laser Beam Machining (LBM) |
Energy Source | Accelerated electrons via high-voltage | Photons (light) |
Mechanism | Utilizes high-velocity electrons to heat and vaporize material | Employs a focused laser beam for melting or vaporizing material |
Energy Transfer | Conversion of electron kinetic energy to heat | Absorption of laser beam energy by the material, causing localized heating |
Penetration Depth | Achieves high depth due to substantial electron energy | Depth depends on laser wavelength and material properties |
Workpiece Material | Applicable to both conductive and non-conductive materials | Versatile, suitable for a diverse range of materials |
Accuracy and Precision | Ensures high accuracy and precision within the micro and nanometer range | Provides high accuracy and precision within the micrometer range |
Heat-Affected Zone (HAZ) | Minimizes HAZ due to the swift conversion of electrons to heat | Results in a smaller HAZ compared to traditional machining but may affect heat-sensitive materials |
Setup Complexity | Requires a vacuum environment and an electron gun | Needs optical components and alignment but does not necessitate a vacuum |
Cutting Speed | Exhibits high cutting speeds owing to the rapid electron velocities | Generally maintains high cutting speeds, albeit not as fast as EBM |
Application Flexibility | Primarily employed for drilling, welding, and cutting of conductive materials | Versatile, used for cutting, welding, engraving, and surface treatment across various materials |
Cost | Involves high initial equipment and maintenance costs | Presents moderately high initial costs with lower maintenance expenses |
Safety | Demands a vacuum chamber and precautions for handling high voltage | Carries lower safety risks, though precautions are necessary for laser exposure |
Beam Focusing | Achieves beam focusing through electromagnetic lenses | Achieves beam focusing using optical components such as lenses and mirrors |
Limitations of Electron Beam Machining
- Material Constraints: EBM is most effective on conductive materials. Non-conductive materials pose challenges as they do not conduct electricity well, making generating the necessary electron beam difficult.
- High Initial Equipment Cost: The setup for EBM involves sophisticated and high-precision equipment, contributing to high initial costs. This cost factor may be a limiting factor for smaller manufacturing operations.
- Depth of Cut Limitations: EBM is more suitable for shallow cuts due to the nature of the material removal process. Achieving deep cuts can be challenging, and other machining processes may be more suitable for such applications.
- Surface Finish: The process may result in a relatively rough surface finish, requiring additional finishing processes to achieve the desired smoothness.
Conclusion
In precision engineering domain, Electron Beam Machining (EBM) emerges as a sophisticated and indispensable technology. Its applications span various industries, from aerospace and automotive to electronics and medical devices, showcasing its ability to meet the exacting demands of modern manufacturing. As technology advances, EBM is likely to play an increasingly pivotal role in shaping the future of precision engineering.
0 Comments