Multi-Material 3D Printing: A Detailed Guide
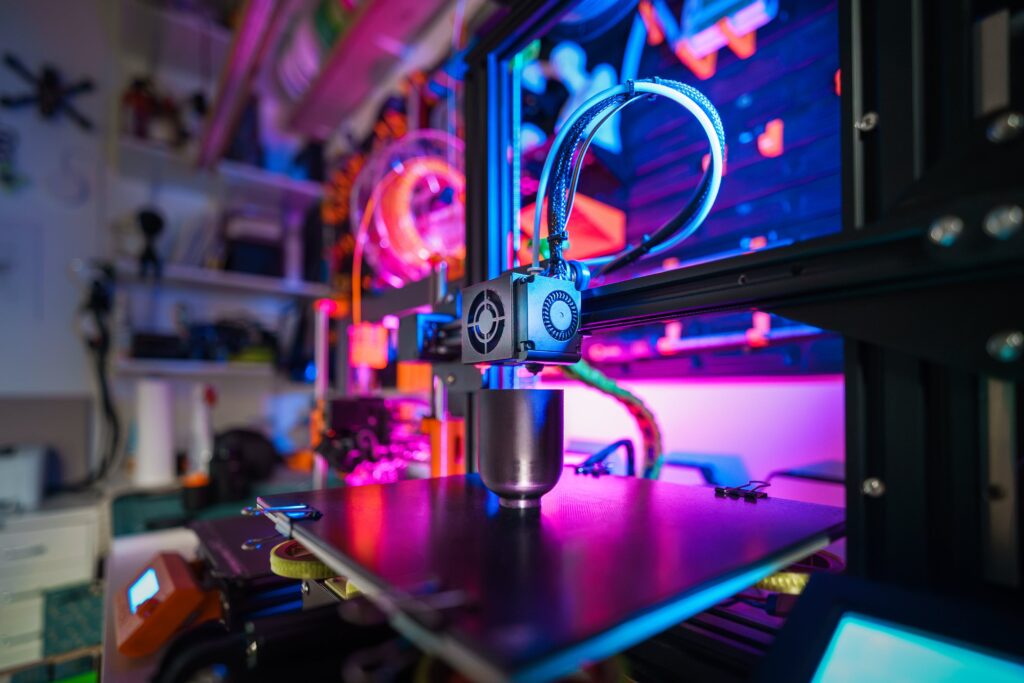
The landscape of additive manufacturing has evolved significantly with the advent of multi-material 3D printing. This cutting-edge technology goes beyond the constraints of traditional single-material printing, ushering in a new era of complex, functional objects with diverse material properties. As we delve into the advanced techniques of multi-material 3D printing, understanding its fundamentals becomes crucial to recognize its pivotal role in additive manufacturing.
Understanding Multi-Material 3D Printing
Multi-material 3D printing, or multi-material additive manufacturing, involves the simultaneous or sequential deposition of multiple materials in a single printing process. Unlike conventional 3D printing, which is restricted to a single material per print job, multi-material printing opens up possibilities by integrating diverse materials within the same object.
Significance of Multi-Material 3D Printing
The significance of multi-material 3D printing lies in its ability to address the inherent limitations of single-material printing. This technology facilitates the formation of complex structures with varying material characteristics, enabling the production of objects with enhanced functionality, improved aesthetics, and customized properties. It excels in traditional manufacturing boundaries by combining materials, such as rigid and flexible elements or conductive components, within a single print.
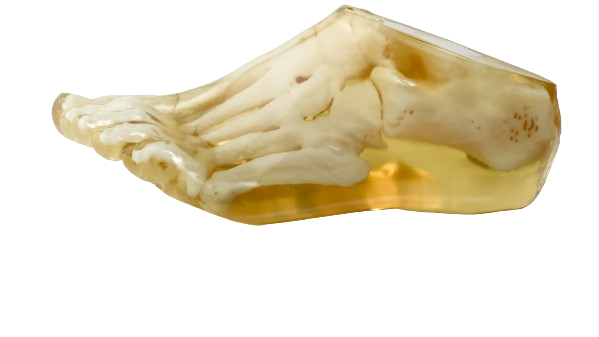
Multi-material 3D Printing Technologies
Fused Filament Fabrication (FFF)
Fused Filament Fabrication (FFF), synonymous with Fused Deposition Modeling (FDM), is a method where thermoplastic material is continuously extruded to form 3D models. The FFF process supports an extensive range of materials, from biodegradable PLA to engineering-grade PEEK and flexible options like TPU.
Single Nozzle Design
In this approach, different materials are combined before or in the melting zone of the print head, extruding through a single nozzle.
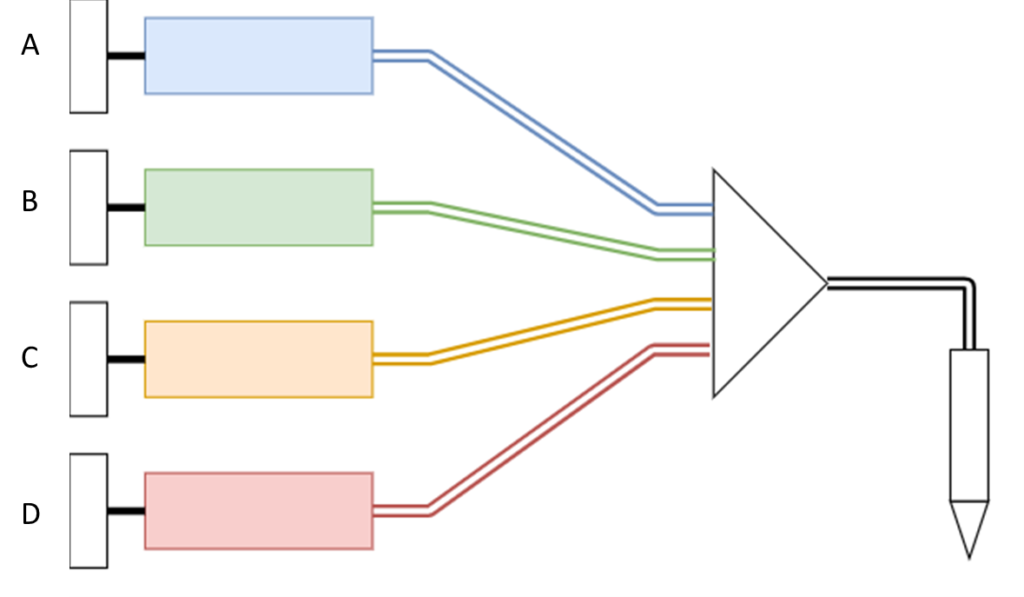
Clearing the melting chamber between materials is necessary, generating some waste material. Some implementations may reuse the previous material as infill or print a different object simultaneously.
Multi-Nozzle Design
In contrast, the multi-nozzle design features a separate nozzle for each material. These nozzles can be mounted on the same print head or on independent print heads. Calibration is crucial to ensuring that the different nozzles are at the exact same height relative to the print surface, preventing interference issues. This design significantly reduces waste material compared to single nozzle configurations.
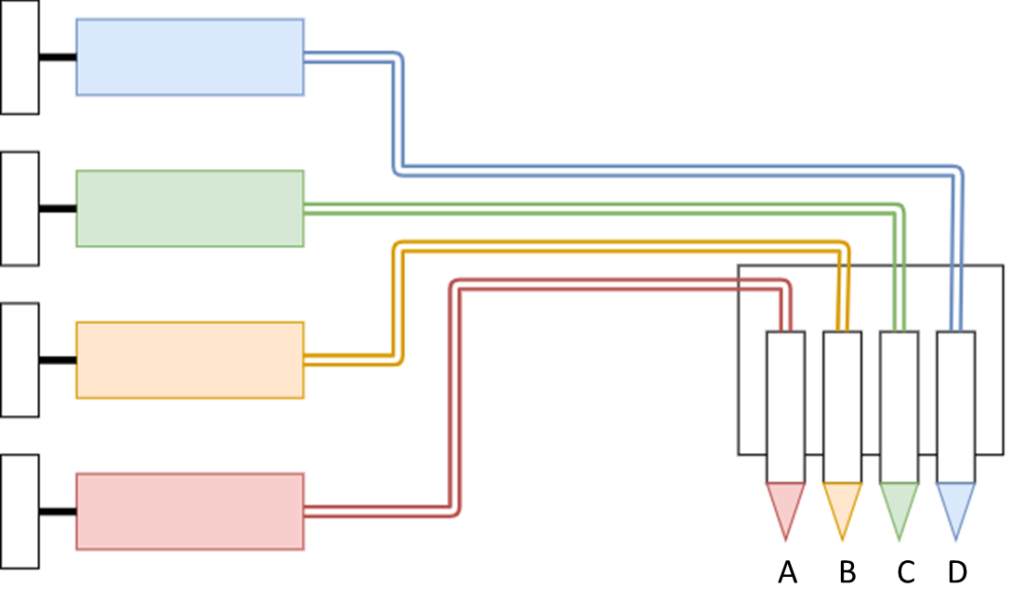
Stereolithography (SLA)
Stereolithography involves solidifying a photopolymer with a laser layer by layer to create 3D objects. Achieving multi-material prints with SLA requires the use of multiple reservoirs for different photopolymers.
This approach presents challenges, particularly in removing not yet polymerized material, as the print may contain cavities filled with the old material. Different photopolymer resins are used in SLA, ranging from standard resins with various colors and opacities to engineering-grade materials and flexible resins.
Material Jetting 3D Printing
Material jetting, often termed Inkjet 3D printing, resembles 2D inkjet printing but in three dimensions. The print head comprises multiple small nozzles that jet droplets of photopolymers on demand.
Each nozzle can extrude a different material, allowing the creation of multi-material parts. The droplets of material are immediately cured using a UV light source mounted to the print head. Unlike the FFF process, layers are formed by scanning the layer line by line. The materials supported by material jetting are similar to those in the SLA process. Additionally, there are advancements in material jetting metals by suspending nanometal particles in a fluid, requiring sintering after support material removal.
Binder Jetting
Binder jetting 3D printing utilizes fine-grained powder fused together with a binder to form a three-dimensional object.
In this process, two chambers are involved: one as a reservoir for powdered material and the other as a printing chamber. To create a layer of an object, a blade pushes the material out of the reservoir and spreads it over the printing surface to form a thin layer of powder. A print head, similar to a 2D inkjet printer, then applies the binder to the layer to solidify and bind it to the previous one. While binder jetting doesn’t inherently allow for multi-material support, some printers feature a second print head to apply pigment to the layer after the binder, enabling full-color prints.
The multi-material 3D printing encompasses various technologies, each with its unique strengths, considerations, and applications. The choice of technology depends on the specific requirements of the intended application, including material characteristics, precision, and the desired level of waste reduction.
Materials for 3D Printing
Multi-material 3D printing often results in superior mechanical performance compared to single-material printing. Robust printing methods, such as micro-additive stacking, ensure layer consistency and enhance surface quality. Choosing materials for multi-material 3D printing involves assessing their machinability, mechanical and physical properties and availability. Key materials like PET, polyethene terephthalate, PA, polyamide, TPU, thermoplastic polyurethane, PC, polycarbonate, and HIPS, high-impact polystyrene, are commonly used due to their versatility and compatibility with various printers. This process allows the creation of components with tailored characteristics through layering different materials.
Applications of Multi-Material 3D Printing
Medical Prototypes with Biomimicry
In the medical field, multi-material 3D printing allows for producing of prototypes mimicking biological structures. This biomimicry enables the development of realistic anatomical models for surgical planning, medical training, and customizing implants or prosthetics. The replication of soft tissues alongside rigid structures contributes to a more accurate representation and testing.
Prototyping Complex Mechanical Assemblies
Multi-material 3D printing revolutionizes the prototyping of complex mechanical assemblies. Engineers can create prototypes closely mimicking the properties of the final product, incorporating different materials for various components. This realism aids in validating designs, assessing functionality, and identifying potential challenges early in development.
Electronics Printing
In the electronics industry, multi-material 3D printing finds a niche. Integrating conductive and insulating materials enables the fabrication of functional electronic components, including circuitry, sensors, and intricate parts with diverse material properties in a single manufacturing process.
Functional Prototypes for Product Testing
Printing functional prototypes with varied material properties allows for comprehensive product testing. From evaluating the durability of moving parts to simulating the behavior of different materials under stress, multi-material 3D printing enables engineers to perform realistic testing scenarios, accelerating the product development cycle and enhancing accuracy in performance predictions.
Customization in Prototyping
Multi-material 3D printing facilitates the creation of highly customized prototypes, tailoring material properties to specific regions based on functional requirements. This level of customization is invaluable in industries where unique designs and tailored functionalities are crucial, such as aerospace or medical device development.
Challenges in Multi-Material 3D Printing
Material Compatibility and Processing Constraints
Achieving compatibility among various materials is intricate due to differences in melting points, rheological properties, and curing processes. Intensive research and development are necessary to formulate material combinations that seamlessly cooperate throughout printing.
Print Head Calibration and Interference
In multi-nozzle designs, meticulously calibrating multiple nozzles to the same height is imperative to prevent interference with the printed object, impacting print quality. Advanced calibration algorithms and technologies must be implemented to automate this process and minimize potential errors.
Waste Reduction and Recycling
Clearing the melting chamber between different materials in single-nozzle designs generates waste material. Techniques need to be developed for repurposing or recycling the waste material produced during the multi-material printing process, reducing its environmental impact.
Removal of Unpolymerized Material in SLA
Stereolithography (SLA) presents challenges in removing material that has not yet been polymerized, especially from cavities. Improved post-processing techniques and material formulations are essential to efficiently remove unpolymerized material efficiently, ensuring clean prints.
Cost and Accessibility
Access to diverse multi-material 3D printing technologies can be limited by cost, hindering widespread adoption. Ongoing research is needed to develop cost-effective multi-material printers and materials, making the technology more accessible to a broader user base.
Conclusion
In conclusion, the advanced techniques in multi-material 3D printing are transforming traditional manufacturing paradigms. From sequential and simultaneous printing methods to innovative powder bed fusion and resin-based approaches, the versatility of multi-material printing opens doors to numerous applications. As we look towards the future, increased automation, improved software interfaces, a broader range of materials, and integration with Industry 4.0 technologies will propel multi-material 3D printing into new frontiers. The ability to create intricate, functional objects with diverse material properties positions this technology at the forefront of innovation impacting industries ranging from healthcare to electronics.
0 Comments