Precision Metal Casting: Revolutionizing Manufacturing with Accuracy
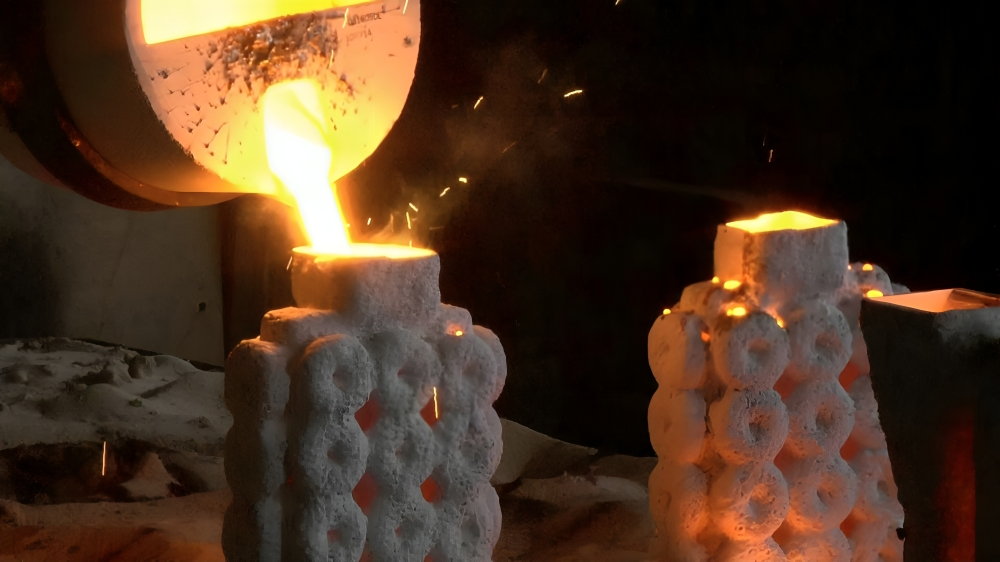
Precision metal casting stands at the forefront of modern manufacturing, offering a sophisticated and efficient method for producing intricate metal components with good accuracy. This advanced casting technique has become a keystone in various industries, revolutionizing how complex metal parts are manufactured. This article will explore the intricacies of precision metal casting, its applications, advantages, and the technological innovations driving its growth.
What is Precision Metal Casting?
Precision metal casting, often called investment casting or lost-wax casting, is a manufacturing process that dates back thousands of years but has evolved significantly with technological advancements. The process begins with creating a wax pattern or replica of the desired metal part. This wax pattern is then coated with a ceramic shell, making a mold to form the metal component.
The wax is melted or “lost” from the ceramic mold, leaving behind a cavity in the exact shape of the intended metal part. Molten metal is then poured into the mold, filling the cavity and taking the shape of the original wax pattern. Once the metal solidifies, the ceramic shell is removed, revealing the final precision-cast metal component.
Applications of Precision Metal Casting
Precision metal casting finds applications across various industries due to its ability to produce intricate and complex metal parts with high dimensional accuracy. Some key sectors leveraging this advanced casting technique include:
Aerospace: Precision casting is widely used in aerospace manufacturing for producing critical components such as turbine blades, engine components, and structural elements. The method’s ability to create intricate shapes with precise tolerances is crucial for the performance and safety of aerospace systems.
Automotive: In the automotive industry, precision casting creates engine parts, transmission components, and intricate brake system elements. The process allows for the production of high-strength and lightweight components, improving fuel efficiency and overall vehicle performance.
Medical Devices: Precision metal casting plays a vital role in producing complex and small-scale medical devices. Components for orthopedic implants, dental prosthetics, and surgical instruments benefit from the accuracy and repeatability offered by this casting method.
Jewelry: The art of precision metal casting has long been a staple in the jewelry industry, where intricate designs and fine details are paramount. Gold, silver, and other precious metals are cast with precision to create exquisite jewelry pieces.
Advantages of Precision Metal Casting
High Dimensional Accuracy: Precision metal casting allows for producing intricate and complex parts with tight tolerances, ensuring high dimensional accuracy and repeatability.
Versatility: The process accommodates a wide range of metals and alloys, offering versatility in material selection to meet specific application requirements.
Reduced Material Waste: The “lost-wax” nature of the process minimizes material waste, making precision casting a more sustainable and cost-effective manufacturing method.
Surface Finish: Precision casting produces parts with excellent surface finishes, eliminating the need for extensive post-processing.
Challenges and Drawbacks of Precision Metal Casting
While precision metal casting offers numerous advantages, it is important to acknowledge the challenges and drawbacks associated with this intricate manufacturing process:
- Cost: Precision metal casting can be more expensive than traditional casting methods due to the complexity of the process, the use of specialized materials, and the need for skilled labor. Initial tooling costs and the intricacies of wax pattern creation contribute to higher upfront expenses.
- Production Time: Precision casting takes longer than traditional casting methods. Creating intricate wax patterns, coating with ceramic shells, and carefully removing the wax adds to the overall production time. This may not be ideal for industries requiring rapid production.
- Limited Size and Weight: Precision casting is generally more suitable for smaller to medium-sized components. The complexity of the process and challenges associated with handling larger molds and heavier metals make it less practical for certain applications.
- Surface Finish Consistency: Achieving consistent surface finishes across multiple castings can be challenging. Variations in the ceramic shell coating or the cooling process may lead to slight variations in the final surface quality.
- Environmental Concerns: The ceramic shell used in precision casting contains binders and refractory materials, which may raise environmental concerns. Proper disposal and recycling of these materials must be managed responsibly.
Precision Casting vs. Sand Casting
Aspect | Precision Metal Casting | Sand Casting |
Tolerance and Accuracy | High precision with tight tolerances | Tolerances may be less precise |
Surface Finish | Superior finishes without extensive post-processing | May require additional machining or finishing |
Complexity of Parts | Well-suited for intricate and detailed components | Limited in replicating high intricacy |
Material Selection | Accommodates a wide range of metals and alloys | More versatile in handling various materials |
Tooling and Setup | Complex setup involving wax patterns and ceramic shells | Generally simpler tooling and setup |
Conclusion
Precision metal casting has emerged as a key player in manufacturing, offering unparalleled accuracy and versatility. Its applications span critical industries, contributing to aerospace, automotive, medical, and jewelry manufacturing advancements. As technology evolves, precision casting is poised to play an even more significant role in creating complex metal components, driving innovation and efficiency in diverse sectors.
0 Comments