Robotics in Industry: Enhancing Efficiency and Precision
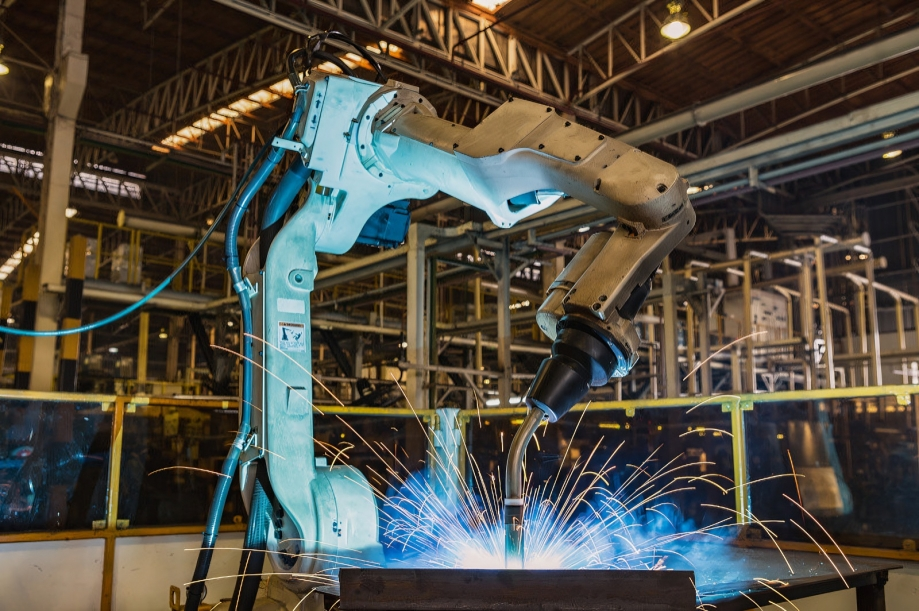
The integration of robotics in fabrication processes has ushered in a new era of efficiency and precision in manufacturing. As industries strive for enhanced productivity and product quality, robotic systems have emerged as indispensable tools. This article explores the impact of robotics on fabrication, highlighting the ways in which these intelligent machines are revolutionizing traditional manufacturing processes.
Historical Context
The utilization of robots in fabrication traces its roots to the mid-20th century, with the advent of industrial robots in automotive assembly lines. Over the years, advancements in technology and artificial intelligence have led to the evolution of these machines, making them versatile and adaptable to various fabrication tasks. Today, robotics in fabrication extends beyond automotive manufacturing, encompassing aerospace, electronics, and construction industries.
Key Applications of Robotics
- Welding and Joining: Robotic welding systems have become integral to fabrication processes, ensuring consistent and high-quality welds. These robots are programmed to handle intricate welding tasks, reaching areas that may be challenging for human operators. Precision in welding contributes to the structural integrity and longevity of fabricated products.
- 3D Printing and Additive Manufacturing: Robotics plays a pivotal role in 3D printing and additive manufacturing. Robotic arms equipped with specialized extruders or deposition heads enable the layer-by-layer construction of complex geometries. This accelerates the fabrication process and allows for the production of intricate and customized components.
- CNC Machining and Milling: Computer Numerical Control (CNC) machines enhance precision and speed in milling and machining processes when integrated with robotic systems. Robotics enables swift tool changes, automated material handling, and the execution of intricate machining operations with minimal human intervention.
- Material Handling and Assembly: Robots excel in material handling and assembly tasks, streamlining the fabrication workflow. Automated guided vehicles (AGVs) and robotic arms work collaboratively to transport materials and assemble components, reducing cycle times and minimizing errors in the assembly line.
- Logistics and Warehousing: Autonomous mobile robots (AMRs) are employed for efficient warehouse material handling, inventory management, and order fulfillment. Drones are utilized for inventory tracking in large outdoor spaces.
- Construction: Robots are used for tasks like bricklaying, 3D printing of structures, and hazardous material handling in construction sites, enhancing efficiency and safety.
Benefits of Robotics in Fabrication
- Enhanced Precision: Robotics, guided by advanced sensors and vision systems, offer unparalleled precision in fabrication. This precision ensures that each component meets exact specifications, resulting in higher product quality.
- Increased Efficiency: Automated fabrication processes significantly reduce production times. Robots operate 24/7 without fatigue, increasing overall efficiency and faster time-to-market for fabricated products.
- Improved Safety: Dangerous or repetitive tasks can be delegated to robots, reducing the risk of workplace injuries. Human workers can focus on supervisory and more complex tasks, creating safer working environments.
- Customization and Flexibility: Robotics in fabrication allow for greater customization of products and increased flexibility in production lines. Rapid reprogramming of robots facilitates the quick adaptation to changes in product design or manufacturing requirements.
AI Improving Robotics Working
Artificial Intelligence (AI) plays a pivotal role in enhancing the functionality of robotics. The integration of AI technologies such as machine learning and computer vision empowers robots with advanced capabilities:
- Machine Learning for Adaptability: AI allows robots to learn from experience and adapt to changing environments. This is particularly beneficial in tasks that involve pattern recognition, enabling robots to improve their performance over time.
- Computer Vision for Perception: Computer vision enables robots to interpret and understand visual information from their surroundings. This enhances their ability to navigate complex environments, identify objects, and make decisions based on visual inputs.
- Natural Language Processing (NLP): AI-driven NLP facilitates communication between humans and robots. This is crucial in collaborative settings where robots need to understand and respond to human instructions or queries.
- Predictive Analytics: AI enables robots to predict and anticipate events, optimizing their decision-making processes. This is valuable in scenarios where robots need to plan and execute tasks efficiently.
Robotics Role in Industry 4.0
Industry 4.0, characterized by the integration of digital technologies into manufacturing processes, relies heavily on robotics and AI for its transformative impact. The key roles of robotics in Industry 4.0 include:
- Smart Factories: Robotics and AI enable the creation of smart factories where machines communicate with each other and with centralized systems. This interconnectedness enhances overall efficiency, reduces downtime, and facilitates real-time decision-making.
- Automated Production Lines: Robotics automates various aspects of production, from assembly and testing to packaging. This automation leads to higher productivity, reduced errors, and improved product consistency.
- Data-driven Decision-Making: Robotics generates vast amounts of data during operations. AI algorithms analyze this data to provide insights, enabling manufacturers to make informed decisions about process optimization, predictive maintenance, and resource allocation.
- Customization and Flexibility: Robotics in Industry 4.0 allows for flexible and customized production. Machines can quickly adapt to product specifications or demand changes, ensuring a more agile and responsive manufacturing process.
Challenges and Future Trends
Integration Costs: While the benefits are significant, the initial costs of integrating robotic systems into fabrication processes can be substantial. However, the long-term efficiency gains often outweigh the initial investment.
Skills Gap: The increasing reliance on robotics necessitates a workforce skilled in programming, maintaining, and supervising these machines. Addressing the skills gap is crucial for widely adopting robotic technologies in fabrication.
Human-Robot Collaboration: Future trends in robotics involve enhancing collaboration between humans and robots. Cobots, or collaborative robots, are designed to work alongside human operators, combining the strengths of automation and human intuition.
Conclusion
Integrating robotics in fabrication represents a transformative shift in manufacturing paradigms. As technology continues to advance, the synergy between human expertise and robotic precision will propel industries towards unprecedented levels of efficiency and product quality. The future of fabrication is undeniably intertwined with the evolution of robotics, promising a landscape where innovation knows no bounds.
0 Comments