Revolutionizing Precision: Unveiling the Future of 5-Axis CNC Machining
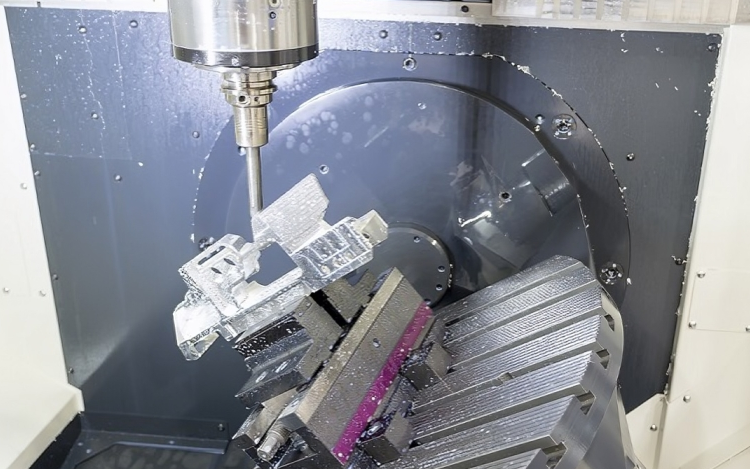
In the dynamic era of precision manufacturing, 5-axis CNC machining emerges as a technological marvel, reshaping the landscape of machining. This article explores the recent strides made within 5-axis CNC machining, offering a profound analysis of its applications, benefits, and the transformative impact it wields over the complex world of precision manufacturing.
For manufacturing professionals and technology enthusiasts seeking cutting-edge insights, this article unveils the transformative advancements and future prospects of 5-axis CNC machining. Dive into precision engineering’s future to stay ahead in the evolving world of manufacturing excellence.
Understanding 5-Axis CNC Machining
5-axis CNC machining is an unparalleled level of manipulation that enables workpieces to traverse along multiple axes for precious cutting operation and shaping. Extending beyond the conventional 3 axes (x, y, z), these machines introduce a dynamic interplay by incorporating a fourth and fifth axis through spindle rotation. The prowess of these machines is delineated by their physical capabilities, CNC drive system intricacies, and the critical role played by controllers in data transfer and processing systems.
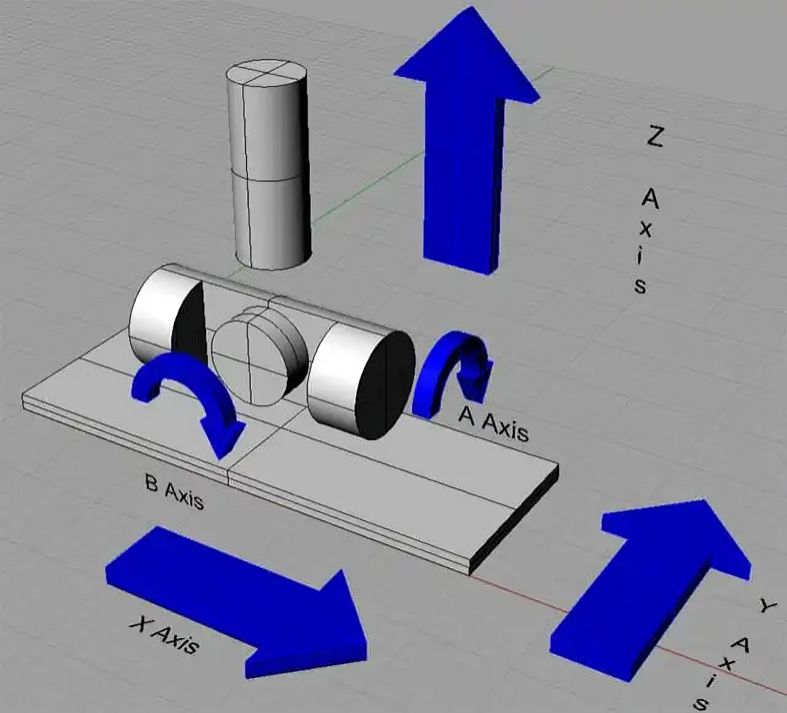
Types of 5-Axis Machines
3+2 Axis Machine
Among the many configurations of 5-axis machines, the 3+2 axis design stands out as a subtype capable of achieving results comparable to its standard 5-axis counterparts. This configuration introduces a tilting rotary table to a vertical machine, an ingenious solution that enhances cutting flexibility while maintaining the workpiece in a static position. Referred to as positional 5-axis machining, this method allows for cuts along the workpiece from multiple angles, unlocking the potential for intricate designs. While offering cost-effectiveness and enhanced substrate stability, this configuration is particularly well-suited for less complex designs.
4+1 Axis Machine
The 4+1 axis configuration emerges as a simplified yet effective approach in the 5-axis machining methods employing stationary axes. In this setup, only a single rotary axis holding the substrate remains in a fixed orientation, creating a surface-independent machining process. This configuration streamlines the dynamic movements of three translational axes and one rotary axis, resulting in a method that maintains a constant cutting angle. This stability increases the predictability of the machining process, particularly beneficial for substrates with cylindrical shapes. While limited in its application scope, the 4+1 axis machine excels in scenarios where constant cutting angles are critical.
Simultaneous 5-Axis Machine
This typical 5-axis CNC machine represents the apex of surface-dependent machining. In this configuration, the cutting tool remains perpetually perpendicular to the substrate, allowing both the movement of the tool along the three primary axes and the rotation of the workpiece along the three rotational axes. This simultaneous movement enables the cutting or milling tool to access and remove material from areas challenging with other 5-axis configurations. As advances in multiaxis machining continue, operating and harnessing the capabilities of simultaneous 5-axis machines becomes increasingly streamlined, making them particularly effective for complex part production.
Challenges of 5-axis CNC Machine
Financial Investment
The adoption of 5-axis machines comes with a considerable financial commitment. The initial acquisition cost of these sophisticated machines is notably high, making them a substantial investment for manufacturing facilities. Additionally, the integration of computer-aided processes and specialized software adds an extra layer of expense. This financial aspect extends beyond the initial purchase, encompassing ongoing maintenance and potential upgrades, contributing to the overall cost of implementing 5-axis machining.
Maintenance Complexity
Maintaining and servicing 5-axis machines pose both financial and operational challenges. The intricacies of these advanced machines demand specialized knowledge and skills, increasing the cost of skilled labor for regular maintenance and troubleshooting. Furthermore, the components and systems involved in 5-axis machines require thorough attention to ensure optimal performance. Any lapse in maintenance can result in downtime, impacting overall productivity and potentially leading to costly repairs.
Operational Intricacies
Operating a 5-axis CNC machine requires a high level of expertise due to the complexity of the machining process. Complex programming is necessary to manipulate the multiple axes and the cutting tool accurately. The trajectory and movement of each component must be precisely calculated and monitored throughout the machining process to ensure accurate cutting and avoid collisions or tool interference. This complexity necessitates skilled labor, contributing to increased labor costs. Additionally, the potential for errors is heightened, emphasizing the need for attention to detail during programming and operation.
Programming Challenges
The trajectory and movement of the cutting tool in 5-axis machines demand sophisticated programming. Geometric operations, toolpath planning, and collision avoidance all add layers of complexity to the programming phase. As designs become more intricate, the intricacy of programming intensifies. This demands not only skilled programmers but also an ongoing commitment to staying abreast of advancements in programming techniques and technologies. The need for specialized expertise in programming adds another layer of challenge to the overall operational landscape.
Risk of Error
The multifaceted nature of 5-axis machining introduces an inherent risk of errors. The slightest miscalculation in programming or oversight during operation can lead to inaccuracies in the finished product. Detecting and rectifying errors in intricate designs can be time-consuming and may result in material wastage. The risk of error further accentuates the importance of skilled personnel and comprehensive quality control measures throughout the machining process.
In navigating these challenges, manufacturers must carefully weigh the benefits against the costs and complexities associated with 5-axis machines, making informed decisions based on their specific operational requirements and long-term strategic goals.
The Future of 5-Axis CNC Machining
As 5-axis CNC machining continues to carve its niche in precision manufacturing, the future promises a trajectory marked by profound technological advancements and innovative transformations:
Smart Manufacturing Integration
The evolution of 5-axis CNC machining aligns with the broader trend of smart manufacturing. Intelligent integration with Industry 4.0 technologies, including the Internet of Things (IoT), artificial intelligence (AI), and big data analytics, will reshape production processes. Real-time data monitoring and analysis will optimize efficiency, enhance quality control, and enable predictive maintenance, ushering in a new era of data-driven precision machining.
Enhanced Automation Capabilities
Anticipated advancements in automation will empower 5-axis CNC machines to handle increasingly intricate processes with a higher degree of efficiency. The integration of robotic systems and advanced control mechanisms will contribute to a seamless and streamlined workflow, reducing manual intervention and elevating the overall automation quotient in precision manufacturing.
Evolution of Cutting-edge Software
The future holds the promise of cutting-edge software that will revolutionize the programming landscape for 5-axis CNC machining. Advanced algorithms and intuitive interfaces will simplify the programming process, making it more accessible to a broader range of operators. This evolution in software will not only increase precision but also facilitate the realization of more intricate and complex designs, pushing the boundaries of what is achievable.
Material Handling Revolution
5-axis CNC machines are expected to expand their material handling capabilities, encompassing a wider range of materials, including softer or more flexible substances. This evolution will open doors to diverse industries, enabling the production of intricate components across sectors such as aerospace, healthcare, and consumer electronics. The ability to navigate a broader material spectrum will enhance the versatility and applicability of 5-axis machining.
Pinnacle of Precision
Technological strides will propel 5-axis CNC machining towards unprecedented levels of accuracy and precision. Continuous refinement in spindle speed, torque, and control mechanisms will result in finer surface finishes, intricate detailing, and tolerances previously considered unattainable. This heightened precision will solidify the position of 5-axis machines as the essence of machining excellence.
Sustainable Manufacturing Practices
The future of 5-axis CNC machining will witness a heightened emphasis on sustainability. Innovations in cutting tools, materials, and energy-efficient machining strategies will contribute to eco-friendly manufacturing processes. This shift towards sustainable practices aligns with the global imperative for environmentally conscious production methods.
As the journey of 5-axis CNC machining unfolds, these anticipated advancements herald a future where precision manufacturing not only meets but exceeds expectations. The synergy of cutting-edge technologies, automation, and a commitment to sustainability will define the next chapter in the evolution of 5-axis CNC machining.
Usage of 5-Axis Machines
- The sweet spot for 5-axis CNC machines lies in the production of intricate designs and components demanding precise measurements.
- In industries like energy and aerospace, where precision is paramount, 5-axis machining finds its niche, adeptly crafting components with complex shapes and stringent tolerances.
- The automotive sector has witnessed a revolution through the induction of multiaxis machining, enabling the production of engines with tighter tolerances, translating to increased horsepower and reliability.
- As technology continues to advance, the applications of multiaxis machining are poised to expand, unlocking possibilities for projects that were once deemed challenging and complex.
Conclusion
5-axis mills and CNC machines have seamlessly integrated into modern manufacturing, becoming indispensable for crafting complex parts with precision. Their efficacy in achieving tight tolerances and high resistance positions them as optimal for diverse manufacturing operations. The single-setup approach of 5-axis machines is rapidly becoming the gold standard, ensuring thorough processing without the need for constant parameter reevaluation. As multiaxis machining evolves, the precision and accuracy achieved by 5-axis machines are poised to become the norm rather than the exception, charting new territories in precision manufacturing.
FAQs
1. What is 5-axis CNC machining?
5-axis CNC machining is an advanced manufacturing technique that allows cutting materials along 5-axis enabling intricate designs and precise components.
2. Who benefits the most from 5-axis CNC machining?
Industries such as aerospace, healthcare, and automotive leverage 5-axis machining for its precision and versatility in producing complex parts.
3. How does Industry 4.0 impact 5-axis CNC machining?
Industry 4.0 technologies like IoT and AI enhance efficiency and quality in 5-axis machining, contributing to the evolution of precision manufacturing.
4. What challenges come with 5-axis CNC machining?
Challenges in adopting 5-axis machining include cost and complexity, but advancements are addressing these issues for broader implementation.
5. What’s the future of automation in 5-axis CNC machining?
The future promises increased automation in 5-axis machines, allowing them to handle intricate processes more efficiently.
6. How does 5-axis CNC machining contribute to sustainability?
5-axis machining supports sustainable practices through eco-friendly cutting tools and energy-efficient strategies, aligning with global environmental goals.
7. Why is precision crucial in 5-axis CNC machining?
Precision ensures accurate and intricate designs in 5-axis machining, with technological advancements continually pushing for higher levels of accuracy.
8. How does software impact 5-axis CNC machining?
Evolving software simplifies programming in 5-axis machining, making it accessible to a wider range of operators and contributing to its widespread adoption.
9. What’s the role of 5-axis CNC machining in the automotive industry?
In the automotive sector, 5-axis machining is crucial for producing components with tight tolerances, contributing to enhanced engine performance and reliability.
0 Comments